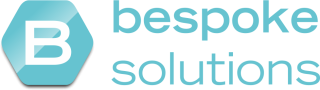
Our partners have gained many years experience within the sanitary and heating industry and with highly trained engineers can develop bespoke solutions in brass and stainless steel enabling us to fulfill many challenging products and applications.
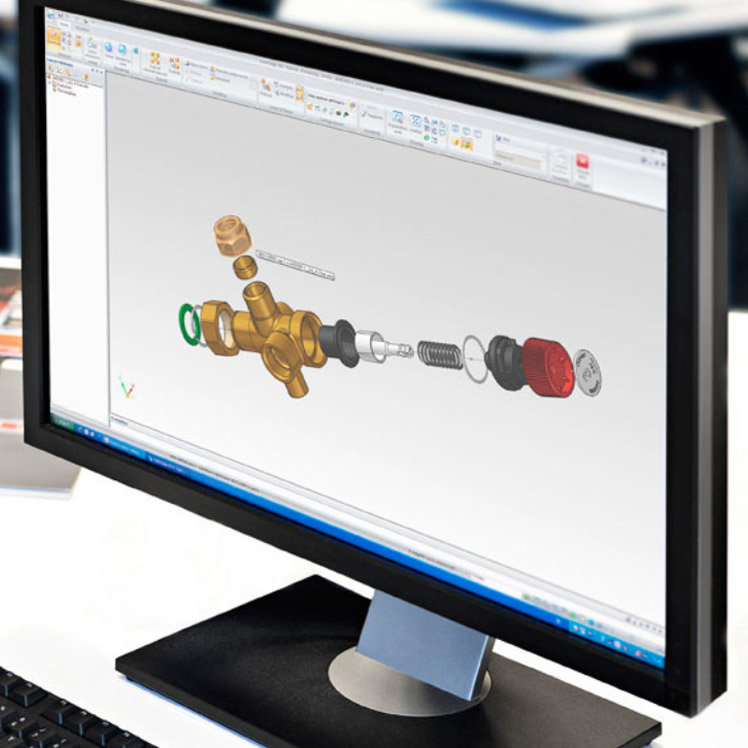
Expansion Vessels
Buffer Tanks
Expansion Vessels
Buffer Tanks
Our partners have gained many years experience within the sanitary and heating industry and with highly trained engineers can develop bespoke solutions in brass and stainless steel enabling us to fulfill many challenging products and applications.
Equipped with fully automated brass hot forging presses, with a capacity
of 550 tons. Able to produce one piece brass bodies up to 100mm (4″).
Composed of Multispindle Automatic Lathes with a high level of production capacity. The machines are capable of pressures between 6 to 8bar and sizes from 6mm diameter to 42mm diameter, simultaneously. CNC single lathes complete the department.
Worked parts arriving from the Transfer and Machining departments are treated in order to remove all impurities and possible working remains, swarf etc. This procedure ensures a high resistance to stain formation, which could develop over time due to humidity. The operation is carried out by a new Centralised Cleaning Machine which uses a modified alcohol based cleaning solution with a wholly vacuum sealed cleaning cycle, up to 999mbar. The technology employed greatly improves cycle time and reduces waste.
Surface treatment is often performed by a high efficiency sand blast machine,
which removes any surface impurities originating from the forming process.
The final results are always a clean, uniform and even surface finish.
Equipped with Vertical and Horizontal Axis Rotary Table Transfer Machines with CNC units and work stations. Automated robotics load and unload machines with integrated Machine Vision Systems.
During all processes a Component Random Sampling system is implemented to ensure constant verification that components are manufactured within tolerance and as requested. Testing procedures are part of a broader quality control concept made from fundamental values which are reflected on each and every stage of the product lifecycle. For this reason we are able to respond to the very highest quality standards world wide, including but not limited to WRAS, TUV, DVGW, GOST. The manufacturing plant for brass components obtained UNI EN ISO 9002 in 1993, later broadening to UNI EN ISO 9001:2008. Advantay also holds the standard ISO 9001:2008.
This department consists of both fully automated and semi automated machinery for assembly, testing and packaging of products. 10 manual assembly areas are used for component assembly of integrated systems and other items.
Factory packaging is carried out by an aided fully automated packaging line.
Packaging and labeling can be customised to customer requirements along with bar coding where required.
With many years experience with OEMs worldwide we are able to develop many kinds of solutions within the field of heating, renewable and sanitary industries from the initial project to the final product. Primarily in brass and stainless steel.
We manufacture components and products for the Solar Thermal, Biomass, Wood Burning, Air and Ground Source applications and for the interface between traditional heating and renewable energy systems.
We produce safety devices, air removal, mixing and control units, connection kits and parts, filling and control valves and drain valves for boiler manufacturers. Stainless steel fabrication includes production of Condensing Units including the full control and testing of the units for OEM customers.
We manufacture brass components, valves and controls for distribution and control of water, gas and other fluids. We manufacture bespoke stainless steel solutions including condensing units and associated parts.
Have an questions? Get in touch with advantay today!
Advantay Ltd
Vantage House
Woodhall Business Park
Sudbury, Suffolk
CO10 1WH
© Advantay Ltd, 2024 | Privacy Policy | Designed by Indigo Ross